Industrial Chillers to RENT, Repair or Service
What is a commercial or industrial chiller and how does it work?
We also cover some of the basic principles of refrigeration.
Where to
What is a Chiller?
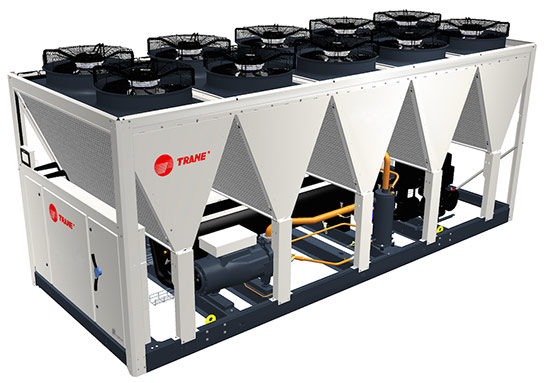
A commercial or industrial chiller is basically an extra-large fridge, just like the one you have at home but many times bigger. It is a refrigeration system used in commercial or industrial facilities like perishable food cold rooms or in a manufacturing plant. Other names for a Chiller are - coolers, refrigerators.
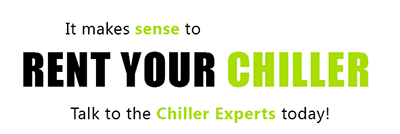
Chiller Rentals for Joburg & Gauteng Areas
How does a Chiller Work?
A chiller removes heat from a liquid by means of a gas compression or absorption refrigeration cycle. This liquid is then circulated through a heat exchanger to cool air, water or equipment as required.
In a refrigeration system, the working fluid is called the refrigerant. Chilled water can also be used as a refrigerant and has a variety of applications from space cooling to process uses.
Let's Talk Business
HVAC SERVICE LEVEL AGREEMENTS ?
Need dependable support and backup at your plant? Then we are the right people to talk to. Obligation FREE consultation.
Different working fluids have different properties and, in choosing one in particular, the designer must first identify the major requirements of the refrigeration system.
Commercial Chillers
Commercial refrigeration systems cover a wide variety of equipment from small "plug-in" vending machines, display cabinets and food service coolers through to large supermarket refrigeration systems.
Users of commercial refrigeration systems need chillers that are reliable and effective, while meeting increasing demands for environmentally friendly solutions.
Chillers Require Maintenance to Operate Best
Regular maintenance to chillers keeps their efficiency high and your investment (and ROI) at its optimum. While technology is advanced and refrigerants are newer and better, it still remains that the working parts require cleaning, inspecting, charging and changing.
The key areas that effect chiller efficiency are:
The most easily overlooked are the normal, everyday and weekly readings. When systems and operations are all 'normal', this is really not considered as a priority, but one that can make all the difference in the long run.
Taking regular readings, however, allows them to watch for trends, possibly catching problems before they result in equipment damage and unexpected downtime.
Industrial Chillers
Industrial refrigeration covers a wide range of applications - from high temperature process chilling to very low temperature applications such as those used in medical freezers.
Industrial chillers are used for controlled cooling of products, mechanisms and factory machinery in a wide range of industries such as:
Chillers for industrial applications can be centralised so that a single large chiller can serve multiple cooling needs. On the other hand, they can be de-centralised so that each application or machine has its own compact chiller. Each approach has its advantages. It is also possible to have a combination of both types of chiller.
At Chiller & Aircon Services we provide environmentally friendly solutions for the entire industrial refrigeration sector.
What Different Types of Chiller Do You Get?
There are three main types of commercial or industrial chiller:
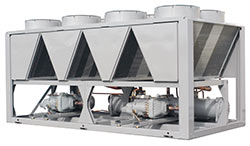
1. Water Cooled Chillers
Chilled water is often used to cool and de-humidify air in mid- to large-size commercial and industrial facilities. Water-cooled chillers are mainly for indoor installation and operation. They are cooled by a separate condenser water loop and connected to outdoor cooling towers to expel heat to the atmosphere. Click here for more details.
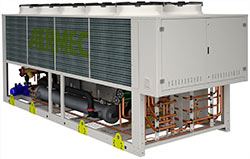
2. Air Cooled Chillers
Air-cooled chillers are installed and operated mainly outdoors. They are directly cooled by ambient air being mechanically circulated directly through the machine's condenser coil to expel heat to the atmosphere. No remote cooling tower is needed.
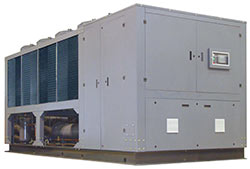
3. Evaporatively Cooled Chillers
Absorption Chillers are powered by a heat source such as steam and has very few moving parts. They have a very low electrical demand but a very high energy (steam) demand.
The Components of a Mechanical Chiller
A mechanical chiller is powered by an electric motor, steam turbine or gas turbine. It has four basic components through which the refrigerant passes:
Let's Talk Business
Need to finance your plant equipment to maximise cashflows? Then we are the right people to talk to. Obligation FREE consultation.
1. Evaporator
The evaporator “exchanges” heat.
It helps heat energy to migrate from a water stream into the refrigerant gas. During this process, the refrigerant absorbs large amounts of heat without changing temperature. Evaporators can be plate type or shell and tube type.
2. Compressor
A compressor pumps the refrigerant gas. The mechanism for compressing gas differs between compressors, and each has its own application. Common mechanical compressors include Reciprocating, Screw, Scroll or Centrifugal. They can be either hermetic (welded closed) or semi-hermetic (bolted together and are normally serviceable).
3. Condenser
The condenser is a heat exchanger which helps heat to move from the refrigerant gas to either water or air. Air cooled condensers are made from copper tubes (for the refrigerant flow) and aluminium fins (for the air flow). Condensers can be air cooled, water cooled, or evaporative.
The Benefits of an Absorption Chiller
The thermodynamic cycle of an absorption chiller is driven by a heat source which is usually delivered by means of steam, hot water or combustion.
Compared to electrically powered chillers, an absorption chiller has a very low electrical power requirement - very rarely above 15 kW combined consumption for both the solution pump and the refrigerant pump.
However, its heat input requirements are large and it needs a much larger cooling tower than a gas-compression chiller. From an energy-efficiency point of view it comes into its own if cheap, high-grade heat or waste heat is readily available. In sunny climates, like we have in Africa, solar energy can be been used to operate absorption chillers.
The absorption cycle uses water as the refrigerant and lithium bromide as the absorbent. The cycle works as a result of the strong affinity that these two substances have for one another. The entire process occurs in almost a complete vacuum.
Well-known compressor brands
We are able to supply and install the following major brands of air-conditioning compressors:
